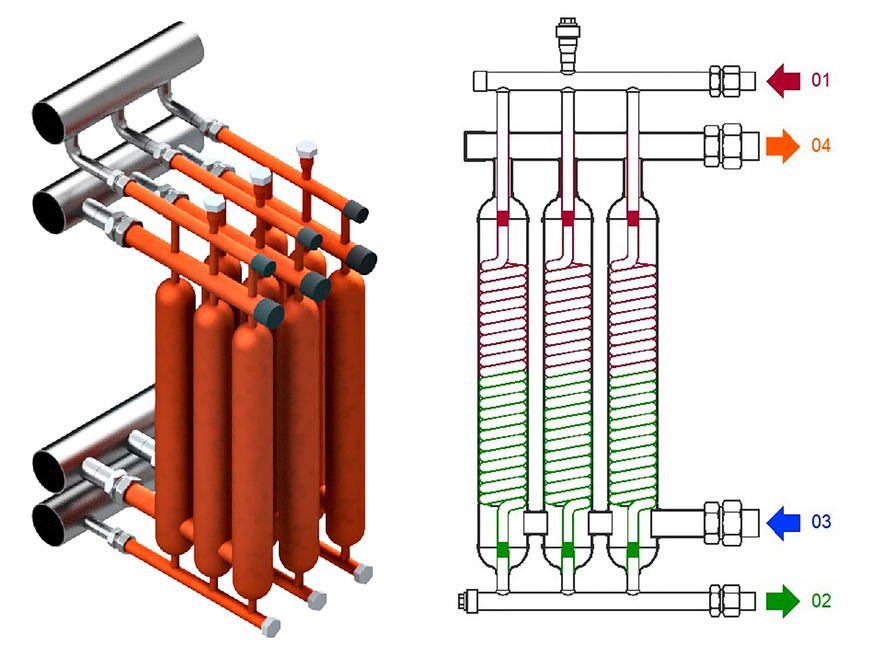
W. Bälz & Sohn
Für die Produktion von Wellpappe wird Pappe mit 180 °C heißem Dampf in Form gebracht und verklebt. Beim Hersteller Kunert Wellpappe wird ein Teil des Dampfes in einem Klarinettensystem zur Beheizung der Halle kondensiert.
Der Artikel kompakt zusammengefasst
■ Bei Kunert Wellpappe ersetzen zwei modular aufgebaute, vollautomatische Dampf-Wärmeübergabestationen Modulo mit einem Klarinettensystem zwei noch funktionstaugliche klassische Dampf-Wärmeübergabestationen zur Wärmeauskopplung für die Hallenheizung.
■ Modulo ist kompakt, kleiner und leichter als die bisherigen Stationen und hat den großen Vorteil, dass sie aus einer flexibel in der Zahl veränderbarer Module besteht. Einzelne Module können sogar bei laufendem Betrieb entnommen und gewartet werden.
■ Durch den geringen Druck/Wasser-Inhalt der Module ist für Modulo keine wiederkehrende TÜV-Prüfung erforderlich. Zudem verringert Modulo durch geringere Wärmeverluste den Energieeinsatz für die Hallenheizung erheblich.
Wellpappe ist ein umweltfreundliches Verpackungsmaterial, denn es besteht aus natürlichen Grundstoffen. Die Coronavirus-Pandemie und die daraus resultierenden Kontakteinschränkungen waren ein weiterer Beschleuniger für das Einkaufen im Onlinehandel. Daraus resultiert ein riesiger Bedarf an umweltfreundlichem Verpackungsmaterial wie Kartons und Schachteln sowie Spezialverpackungen, oder auch Schwerlast- und Gefahrgutverpackungen – alles aus Wellpappe.
Kunststoffverpackungen werden schon seit einiger Zeit aus Umweltschutzgründen mehr und mehr vermieden. So ist umweltschonende Wellpappe aus unserer modernen Art zu leben und einzukaufen nicht mehr wegzudenken. Ihr Hauptbestandteil ist Altpapier aus Recycling-Prozessen, dem zusätzlich Halbzellstoff aus Altholz und Durchforstungsholz beigemischt wird. Die Kartons können also mit gutem Gewissen möglichst mehrfach verwendet und dann wieder dem Recycling zugeführt werden.
Die Produktion von Wellpappe benötigt 180 °C heißen Dampf
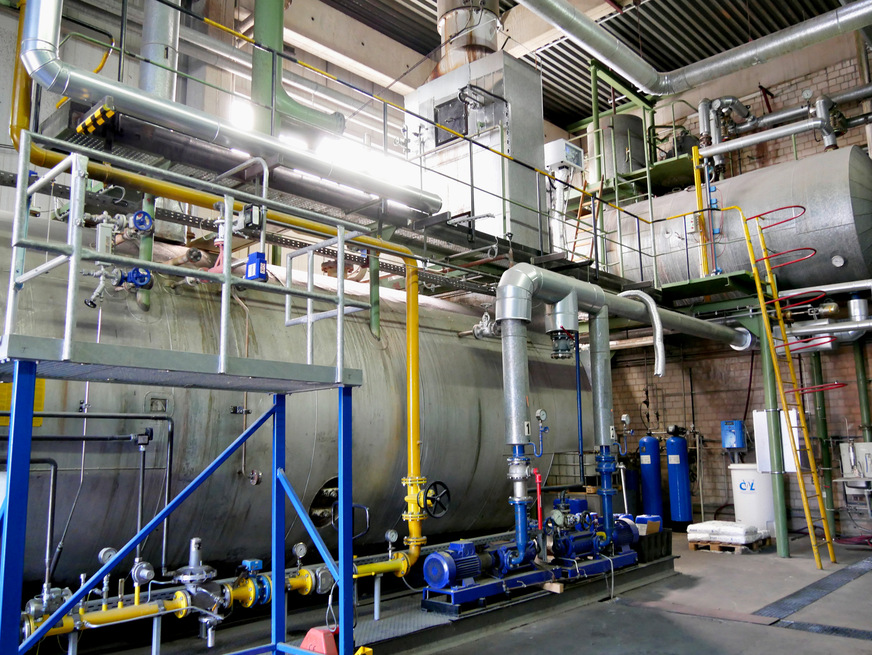
W. Bälz & Sohn
Ausgangsmaterial für die Herstellung von Wellpappe ist Rohpapier, welches in Papierfabriken aus den genannten Materialien hergestellt und dem Produktionswerk in großen Rollen zugeliefert wird. Je nach benötigter Stabilität besteht die Wellpappe aus mehreren Lagen. Zwischen den inneren und äußeren glatten Deckbahnen liegen eine oder mehrere Wellenbahnen.
Um aus glattem Rohpapier Wellenbahnen zu fertigen, wird es unter Druck mittels Riffelwalzen in Form gebracht. Eine oder beide der Riffelwalzen werden beheizt. Die Verformung wird durch Vorbereitung mit Feuchtigkeit (Wasserdampf) und Wärme unterstützt, indem die Wellenbahn über eine Vorheiz- und Befeuchtungsvorrichtung in Form eines drehenden Zylinders (Vorbereiter) läuft. Zur Vorbereitung der Deckenbahn ist nur Wärme erforderlich, ihre Aufheizung erfolgt durch die Umschlingung eines dampfbeheizten Zylinders (Vorheizer).
Zur Erwärmung der Zylinder und Walzen wird Wasserdampf mit einer Temperatur von ca. 180 °C verwendet. Die Wärme wird auch benötigt, um den anschließenden Klebevorgang zu beschleunigen. 180 °C heißer Dampf ist für die Herstellung von Wellpappe also eine Grundvoraussetzung. Bei Kunert Wellpappe in Biebesheim wird er mit großen gasbefeuerten Dampfkesseln selbst erzeugt (Bild 2).
Dampf-Wärmeübergabestationen
Um sich eine zusätzliche Heizungszentrale für die Beheizung der Produktionshallen zu sparen, wird ein Teil des Dampfes für Heizzwecke ausgekoppelt. Das empfiehlt sich schon aus Platzgründen, aber auch durch einen wesentlich besseren Wirkungsgrad mit nur einer Energiezentrale.
Bereits seit Anfang der 1980er-Jahre wird bei Kunert Wellpappe ein Teil des für die Produktion erzeugten Dampfs in Dampf-Wärmeübergabestationen kondensiert. In dem Wärmeübertrager gibt der kondensierende Dampf seine Wärmeenergie sekundärseitig an das Heizungswasser für die Beheizung der Produktionshallen ab.
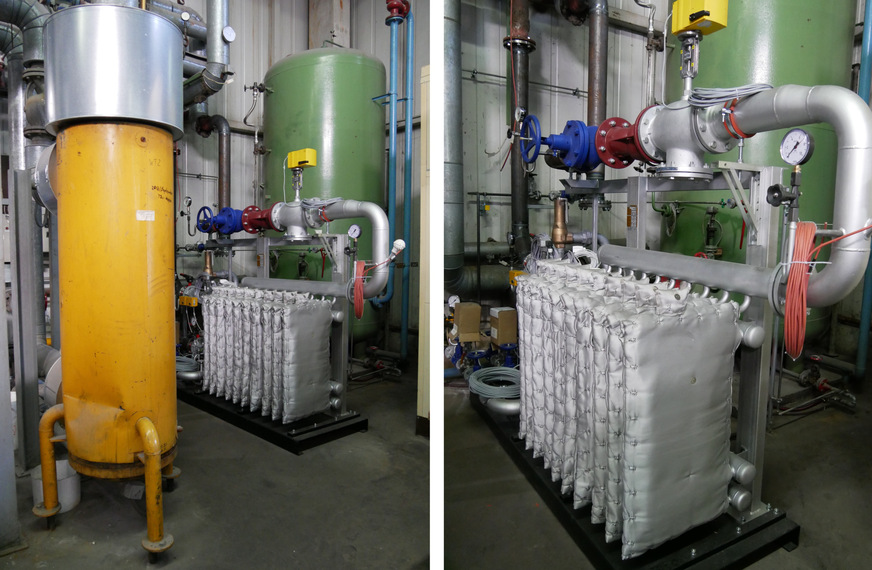
W. Bälz & Sohn
Das Kondensat der Dampf-Wärmeübergabestationen wird mittels Dampfdruck direkt zum Entgaser gedrückt und läuft von dort zum Dampfkessel zur erneuten Dampferzeugung zurück.
Dampf-Wärmeübergabestationen sind geschlossene Dampf-Kondensat-Systeme, ohne Kondensatbehälter [1, 2]. Die seit 1984 verwendeten stehenden Stationen (Bild 3 links), mit einem Mantel aus Stahl und innenliegenden Kupferrohrwendeln bieten eine größtmögliche Wärmeübertragung bei vergleichsweise geringem Platzbedarf: Der Dampf strömt von oben in den Behälter und kondensiert entlang der Kupferrohre unter hohem Druck bis er den Behälter als Kondensat wieder verlässt.
Durch das Konstruktionsprinzip mit einem großen Druckbehälter mussten an den Stationen alle 5 Jahre TÜV-Prüfungen stattfinden. Diese sind aufwendig, da jede Station für die Zeit der Prüfung abgeschaltet und komplett ausgebaut werden muss. Obwohl die Stationen ihren Zweck zuverlässig erfüllten, entschied man sich kürzlich für ein moderneres, flexibleres System, um die organisatorischen und finanziellen Nachteile der TÜV-Prüfungen zu vermeiden: Eine modulare Dampf-Wärmeübergabestation Modulo mit einem sogenannten Klarinettensystem (Bild 1). Die Station mit zehn Modulen (Bild 4) hat eine der beiden bisher in Betrieb befindlichen Dampf-Wärmeübergabestationen ersetzt.
Klarinettensystem Modulo
Das technische Prinzip der Dampfkondensation entspricht exakt dem bisherigen, findet aber nun in wesentlich kleinerem Maßstab statt. In jeder der drei einzelnen mit Dampf beaufschlagten Kupferröhren (Mantel) pro Modul befinden sich im Inneren vom Heizungswasser durchströmte Kupfer-Spiralrohre zur optimalen Wärmeübertragung bei der Kondensation. Der große Vorteil dieser Bauweise ist, dass die Module sehr klein sind und der Druck/Wasser-Inhalt der Kupferröhren sehr gering ist. Deshalb entfällt die sonst gesetzlich vorgeschriebene und für den Betreiber sehr aufwendige TÜV-Prüfung.
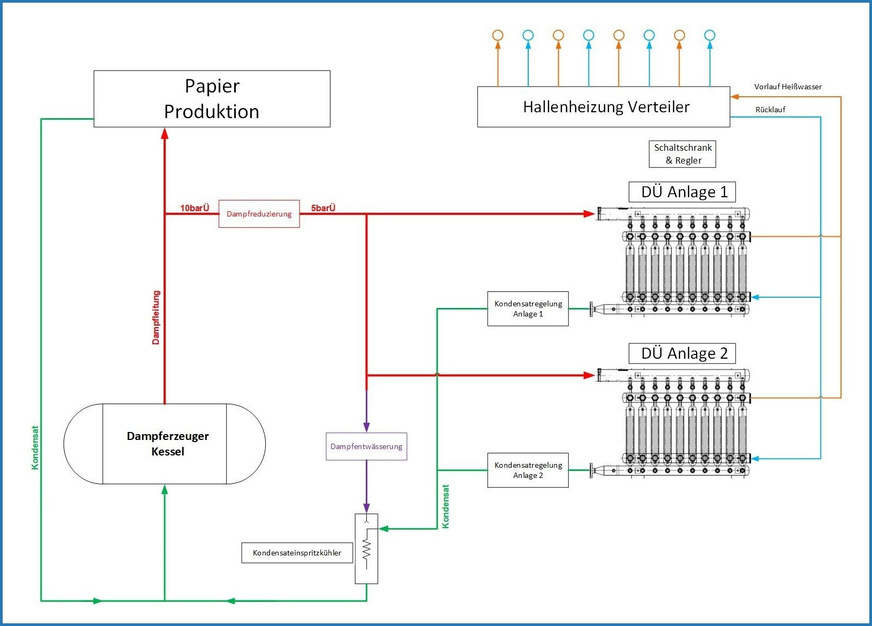
W. Bälz & Sohn
Die für die bisherige Station benötigten 2,4 MW reduzieren sich durch die besonders niedrigen Wärmeverluste der neuen Anlage auf 2 MW Primärenergieverbrauch. Sie ist also auch energetisch deutlich günstiger und es muss somit weniger Gas für die Hallenheizung eingesetzt werden. Modulo ist außerdem sehr kompakt, hat geringere Abmessungen und ein geringeres Gewicht.
Für die Praxis gibt es einen weiteren großen Vorteil: Die Module sind einzeln und bei laufendem Betrieb schnell austauschbar. Beispielsweise für die Wartung können sie in sehr kurzer Zeit einzeln entnommen werden, was zu einer optimalen Verfügbarkeit der Anlage führt. Es kann aber auch jederzeit eine dem aktuellen Bedarf angepasste Veränderung über die Zahl der Module vorgenommen werden. Die Leistung ist so je nach aktuellem Bedarf veränderbar, sowohl durch Entnehmen als auch durch Zufügen von Modulen.
Diese positiven Eigenschaften der Dampf-Wärmeübergabestation Modulo führten inzwischen dazu, dass auch die zweite der ursprünglichen Dampf-Wärmeübergabestationen durch eine Modulo ersetzt wird. Bild 5 zeigt bereits das sehr vereinfachte Anlagenschema mit zwei Modulo-Stationen. Die Beheizung der Produktionshallen ist damit noch deutlich energiesparender als mit den bisherigen Dampf-Wärmeübergabestationen.
Literatur
[1] Bälz, U.; Kilpper, R.: Energieeinsparung durch effiziente Dampf-Kondensat-Systeme. Berlin: Huss-Medien, Moderne Gebäudetechnik 03-2013
[2] Kilpper, R.; Wintgens, C.: Dampfenergie optimal ausgenutzt. Stuttgart: Gentner Verlag, Die Kälte und Klimatechnik 07-2020