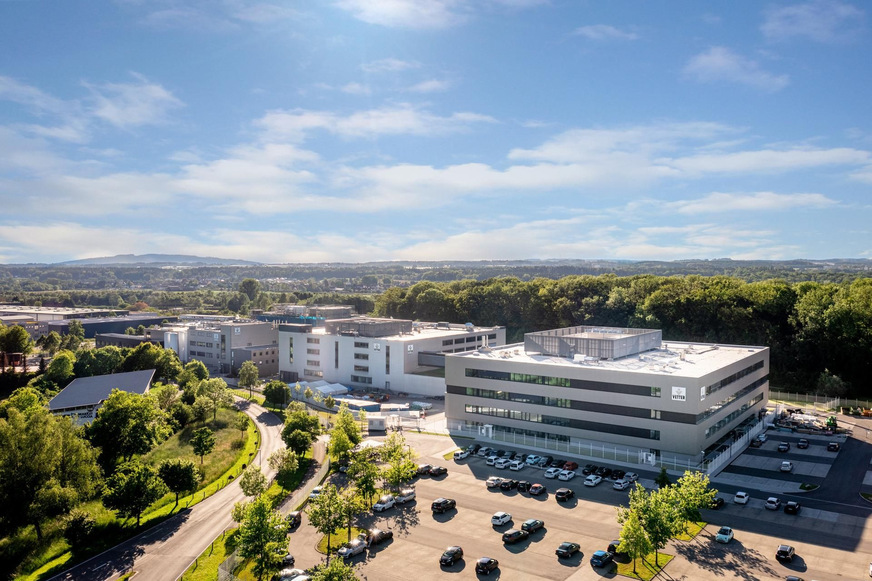
Pharma Vetter
Hohe Verfügbarkeit und konstante Temperaturführung sind zentrale Anforderungen an die Kälteversorgung in der Pharmaproduktion. Pharmadienstleister Vetter hat am Standort Ravensburg in Zusammenarbeit mit Carrier vier Kälteanlagen in zwei hydraulischen Systemen in Betrieb genommen, die diese Anforderungen erfüllen. Die Anlagen wurden nach dem Regelwerk der Pharmaindustrie projektiert, gefertigt und installiert.
Als eine führende „Contract Development and Manufacturing Organisation“ (CDMO) der Pharmaindustrie produziert Vetter mit Hauptsitz in Ravensburg im Kundenauftrag unterschiedlichste Medikamente. Ein Schwerpunkt liegt dabei auf der sterilen Abfüllung von Vials, Spritzen, Karpulen und anderen Injektionssystemen.
Das 1950 gegründete und weiterhin in Familienbesitz befindliche Unternehmen beschäftigt mehr als 6600 Mitarbeitende und wächst kontinuierlich weiter. Mit jedem Produktionsbereich, der in Betrieb geht, wird eine neue und individuell projektierte Kälteversorgung installiert. Denn viele Prozesse der Pharmaproduktion sind temperaturgeführt, und die Produktionsabläufe in der Branche stellen sehr hohe Anforderungen an Verfügbarkeit und Regelgenauigkeit.
Präzise Kälteversorgung für die „End-of-line“-Prüfung
Vetter hat bereits in mehreren Projekten der Kälteversorgung mit der Carrier Klimatechnik zusammengearbeitet. Dabei gehören nicht nur die Auslegung und Produktion der Anlagen zum Liefer- bzw. Dienstleistungsumfang, sondern auch deren Projektierung sowie die Ausarbeitung des Regelungskonzeptes – so auch beim aktuellen Projekt im Werk Ravensburg.
In einem neuen Produktionsbereich mussten Kühlräume, in denen die (Zwischen-)Lagerung vor der optischen Qualitätsprüfung der hergestellten Pharmazeutika stattfindet, auf einem Temperaturniveau von 5 °C gehalten werden. So fordern es die Richtlinien und auch die hohen Qualitätsvorgaben von Vetter für diese pharmazeutischen Produkte.
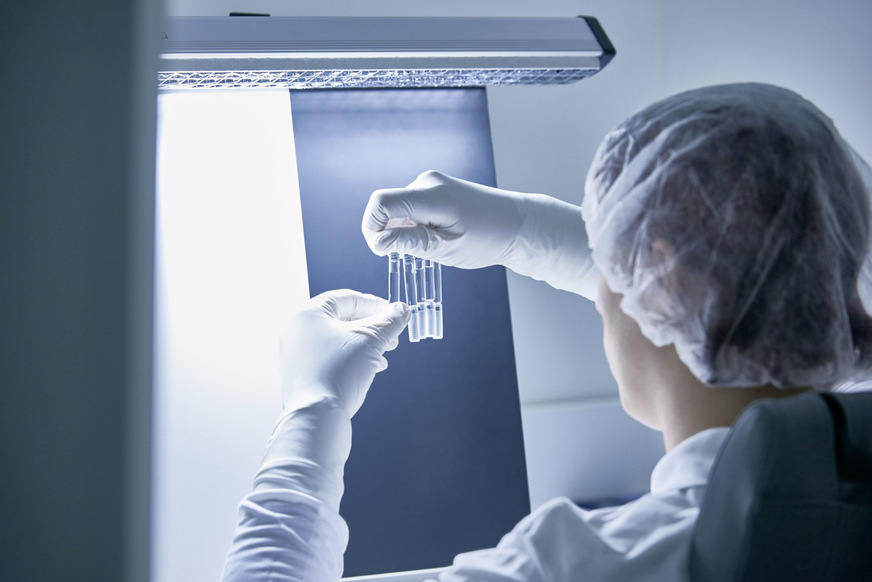
Pharma Vetter
Aus den Kühlzellen zu den Prüfplätzen
Der Prozess sieht vor, dass die produzierten und verpackten Pharmazeutika in Kühlzellen zwischengelagert werden, bevor eine abschließende optische Kontrolle erfolgt. Um die Wege kurz zu halten, befinden sich die Prüfplätze gleich gegen-über der Kühlzellen. Das ist eine von vielen Maßnahmen, die bereits in der Projektierung getroffen wurden, mit dem Ziel, die Kühlkette keinesfalls zu unterbrechen.
Die Anforderungen an die Regelgenauigkeit und die Ansprechgeschwindigkeit der Regelung sind hier sehr hoch. Konkret: Der Kaltwassersatz muss eine konstante, sich nicht zu schnell ändernde Vorlauftemperatur halten, damit auf der Verbraucherseite die Ausregelung der Kühlraumtemperaturen problemlos umgesetzt werden kann. Dabei wird u.a. der Vorlaufsollwert der Kaltwassersätze variabel im Bereich von -5 °C bis -9 °C verschoben. Auch beim Schallpegel und anderen Anlagenparametern hatten die Planer von Vetter sehr konkrete Vorstellungen.
Für diese Aufgabe projektierte Carrier eine Kälteversorgung, die aus vier identischen Kälteanlagen vom Typ 30WG110 mit einer Kälteleitung von je 64 kW besteht. Diese Anlagen zeichnen sich u.a. durch kompakte Bauform und hohe Effizienz aus. Jeweils zwei von ihnen sind mit einem Rückkühler vom Typ 09PE – einem Sole-Luft-Wärmetauscher mit Axiallüfter – kombiniert. Sie bilden eine Einheit, die je einen Solekreislauf mit Kälte versorgt.
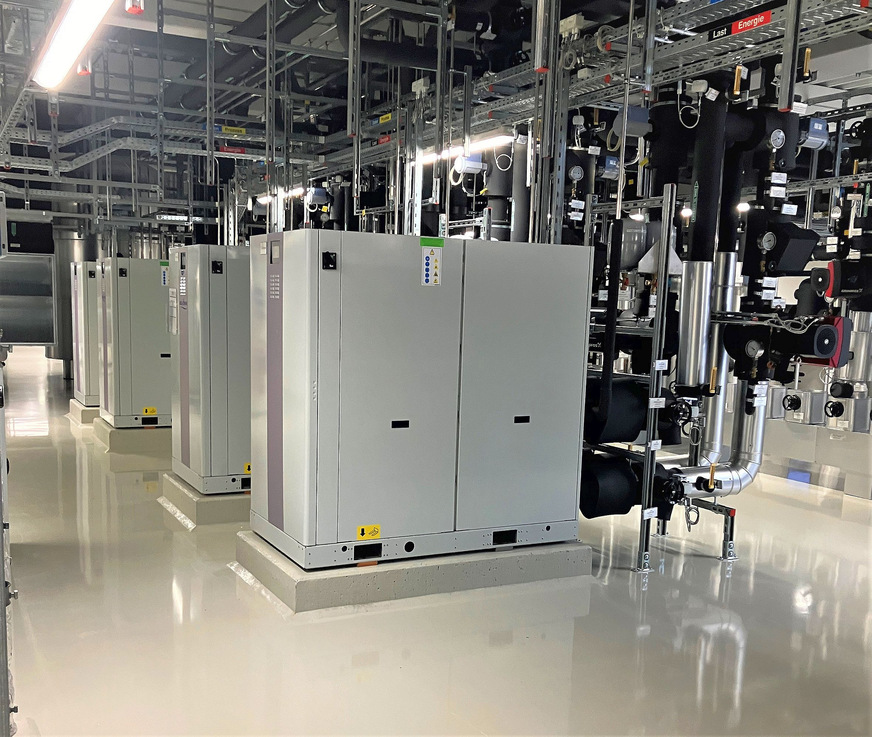
Pharma Vetter
Gemeinsame Projektarbeit
Denis Traub, Infrastructure and Building Automation bei Vetter: „Dieses dezentrale Konzept gewährleistet die geforderte hohe Verfügbarkeit von 99,9 %. Bei einem Ausfall steht immer eine Backup-Anlage bereit, und es wird sofort automatisch umgeschaltet. Zugleich können wir durch die Kaskadierung einen effizienten Betrieb der Kälteversorgung im Teillastbereich sicherstellen.“
Auf der Basis der sehr genauen Vorgaben von Vetter erarbeitete Carrier zunächst ein R+I-Schema, das in intensiver Detailarbeit abgestimmt wurde. Traub: „Wir haben sehr präzise Vorstellungen und auch hohe eigene Kompetenz in Sachen Kältetechnik.“ Entsprechend detailliert waren die Grundlagen, die den Mitarbeitern von Carrier für die Projektierung bereitgestellt wurden.
Kundenspezifische Anpassung
Die im Carrier Werk in Montluel/Frankreich gefertigten Anlagen wurden vom Team in Deutschland an die individuellen Anforderungen angepasst. Die ebenfalls individuell projektierten und in Deutschland gebauten Schaltschränke für die übergeordnete Regelung entsprechen den Spezifikationen von Vetter.
Die Abnahme der neuen Anlagen fand vor Ort bei Carrier statt. Robert Gnatz, zuständiger Projektmanager von Carrier: „So haben wir Zeit gespart und auch die Arbeitsabläufe bei Vetter nicht beeinträchtigt. Außerdem haben wir wesentliche Komponenten schon vor der Montage geprüft, um die Abnahme und Inbetrieb-nahme möglichst effizient zu gestalten.“
Auch ein „Stresstest“ unter Extrembedingungen war Teil des Abnahme- und Inbetriebnahme-Paketes, das nach den in der Pharmaproduktion üblichen strengen Regularien erfolgte. Steffen Bornschlegel, stv. Vertriebsleiter Süddeutschland von Carrier: „Die Anforderungen sind hoch – in der Projektierung, in der Ausführung und in der Inbetriebnahme. Das ist eine Herausforderung, die wir gern annehmen. Und wir schätzen es sehr, dass die Gespräche immer auf fachlich hohem Niveau sind.“
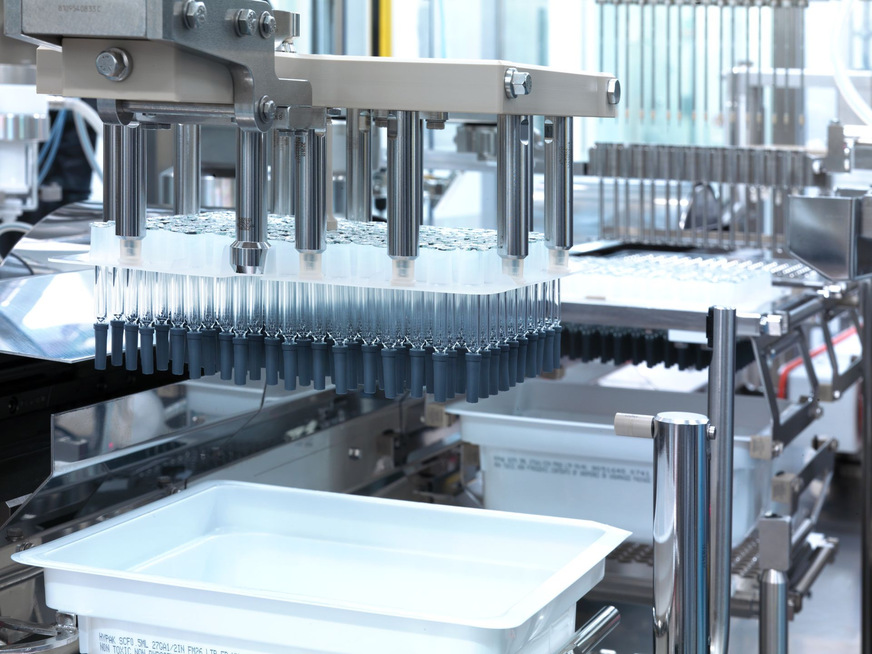
Pharma Vetter
Übergeordnete Regelung an den Einsatzfall angepasst
Geregelt werden die neuen Kälteanlagen durch eine übergeordnete Regelung, die auch die aktuell abgerufene Leistung und die Wärmemengen auf der Kalt- und Kühlwasserseite erfasst. Auch hier handelt es sich nicht um ein Standardsystem, sondern um eine kundenspezifische Entwicklung bzw. Programmierung des Carrier-Geschäftsfelds „Controls.“ Die Regelungs-Experten konnten dabei auf das Gebäudeautomationssystem WebCTRL zurückgreifen, das die Carrier Tochtergesellschaft Automated Logic entwickelt hat. Dieses System ermöglicht eine maßgeschneiderte Regelung von HLK-Anlagen – auch dann, wenn es um hoch spezialisierte und sicherheitskritische Anlagen geht, wie es bei Vetter der Fall ist.
Alle erfassten Werte werden vor Ort anschaulich auf einem Bedienpanel visualisiert, dokumentiert und via Profinet-Anbindung übergeben. Markus Dreher, Projektingenieur bei Vetter: „Die Steuerung ist auch an unser Energiemanagement-system angebunden. Darüber hinaus nutzen wir die Werte zum Systemmonito-ring, d.h. zur vorbeugenden Instandhaltung.“
Grundsätzlich bietet Carrier Controls bei derartigen Regelungsprojekten ein Monitoringsystem an, das einen schnellen Support des Betreiberpersonals ermöglicht. So können Ausfallzeiten auf ein Minimum reduziert und Anlagen im echten Re-gelbetrieb optimiert werden.
Dabei galt es eine Besonderheit zu beachten. Dreher: „Wegen der hohen Security-Anforderungen in der Pharma-Industrie gibt es bei unseren Anlagen keine Kommunikation nach außen.“ Deshalb kam das Monitoring System von Carrier nur während der Inbetriebnahme zum Einsatz, in der die Systeme auf die Kundenanforderungen optimiert wurden.

Pharma Vetter
Wartung vor Ort und unter hohen Sicherheitsanforderungen
Neben den baulichen und steuerungstechnischen Voraussetzungen, die getroffen wurden, um die geforderte hohe Verfügbarkeit sicherzustellen, hat Vetter mit Carrier einen Wartungsvertrag abgeschlossen. Er beinhaltet, dass die Anlagen regelmäßig überprüft und abweichende Parameter korrigiert werden. Für den Fall der Fälle lagern definierte Ersatzteile direkt vor Ort. ■
Quelle: Carrier / fl