Schon seit längerem investiert IMI Hydronic Engineering in die Verbesserung der Energienutzung in seinem Werk in Erwitte, auch werden Photovoltaikanlagen installiert. Das Unternehmen möchte die Verbesserung noch weiter vorantreiben, muss dazu aber wissen, wie sich die Energie im Einzelnen verteilt, d.h. wieviel Wärmeenergie im gesamten System des Werkes fließt und wo wieviel verbraucht wird. Um hierfür präzise Ergebnisse zu erhalten, wurde ein einmonatiger sogenannter „Proof of Concept“, also eine Machbarkeitsstudie, im Erwitter Werk durchgeführt. Zuständig für die Durchführung war das HyInsight-Team von IMI Hydronic Engineering, das im Rahmen der unternehmenseigener Nachhaltigkeitsagenda innovative Lösungen für Überwachung und Reduzierung des CO2-Fußabdrucks und der Energiekosten von Gewerbe- und Industriegebäuden entwickelt. Zusammen mit Enerbrain, einem italienischen Start-up für Optimierungen von HLK-Systemen, sollte die beste Lösung gefunden werden, die einen minimalen Energieverbrauch sowie eine Komfortoptimierung gewährleistet. Um das ganze System zu verbessern, wurde eine optimierte Hydroniklösung, basierend auf TA-Smart, zusammen mit dem von Enerbrain entwickelten Gebäudemanagement in dem Produktionswerk implementiert. Die Produktlinie TA-Smart von IMI Hydronic Engineering, das Durchgangsregelventil mit einzigartiger EQM-Charakteristik mit der Möglichkeit zur Durchfluss-, Temperatur- und Leistungsmessung, kam 2021 auf den Markt Dessen Ultraschall-Durchflussmesstechnologie kombiniert mit den einzigartigen Algorithmen des Antriebes führt zu besten Regelergebnissen. TA-Smart kann entweder den Durchfluss oder die Leistung regeln, bietet hohe Flexibilität in der Anlage und liefert hohen Komfort bei bester Effizienz in Heizungs- und Kühlungsanwendungen. Seine kompakte Bauweise und die einfache Parametrierung reduziert die Einbau- und Inbetriebnahmezeit.
Ausgangslage
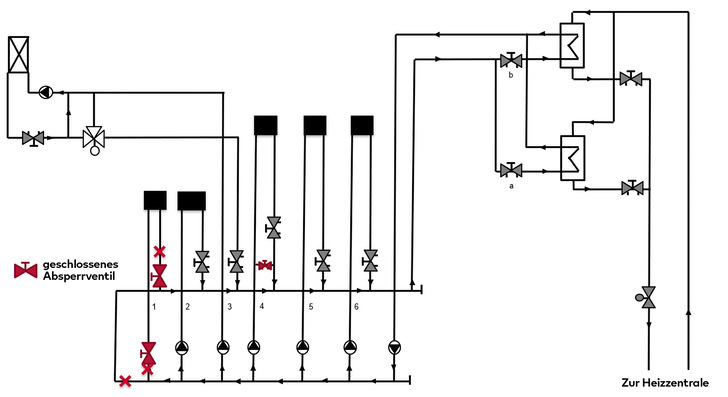
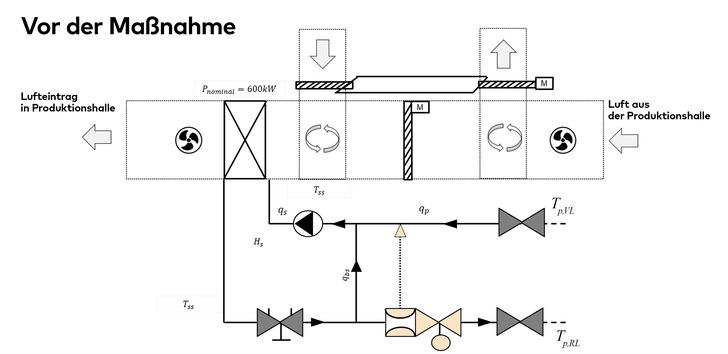
Die Heizwärme für den Erwitter Produktionsstandort wird in einer Heizzentrale erzeugt. Zwei Wärmetauscher sorgen für die Verteilung vom Primär- zu den Sekundärkreisläufen. Danach sind sechs Verbraucher mit unterschiedlicher Last und unterschiedlichen Anforderungsprofilen angeschlossen. Als größter Verbraucher wurde eine Lüftungsanlage (AHU) identifiziert, die eine Leistung von 600 kW hat und damit 80 % der Last in Anspruch nimmt. Die Anlage ist auch für die Beheizung und Umluft der gesamten Produktionshalle verantwortlich. Das Team, das die Machbarkeitsstudie durchführte, konnte anfangs nicht abschätzen, wie viel Energie benötigt und verbraucht wurde. Die Lüftungsanlage und ihre Wärmeübertrager waren überdimensioniert, so dass eine geringe Regelbarkeit des Durchflusses bestand. In den meisten Fällen war die Last so klein, dass das Regelventil kaum geöffnet war, was die Möglichkeit einer genauen Regelung erschwerte. Während der COVID-Pandemie wurde die Hallennutzung am Standort kontinuierlich optimiert und angepasst. Dieses führte zu Herausforderungen bei der Einstellung der richtigen Heizzyklen, denn diese mussten nach Bedarf ständig geändert werden. Es kam so zu Lastschwankungen.
Systemaktualisierung
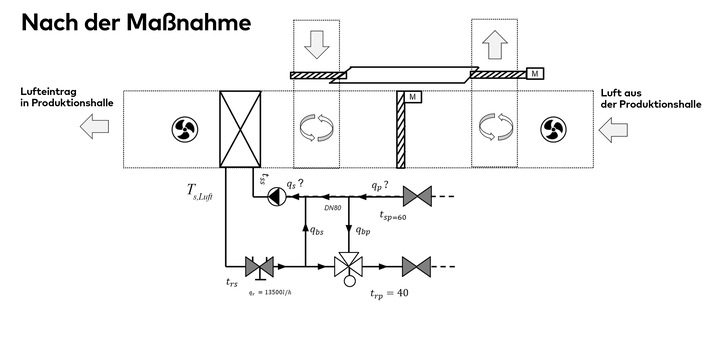
Um sicherzustellen, dass die Produktion über einen längeren Zeitraum nicht gestört wird, musste das System-Upgrade und die Verrohrung in kürzester Zeit durchgeführt werden. Das HyInsight-Team entschied sich dafür, zwei kritische Systemaktualisierungen vorzunehmen. So wurde anstelle des vorhandenen 3-Wege-Mischventils ein TA-Smart installiert. Der Bypass wurde geschlossen, damit die 3-Wege-Schaltung in eine 2-Wege-Schaltung umgewandelt werden konnte. Gewählt wurde ein DN 80 PN-16-Ventil, um die vorhandene Verrohrung anzupassen. Ermöglicht wurde dies durch die hervorragende Regelfähigkeit des Ventils - der Auslegungsdurchfluss macht 28 % des Nenndurchflusses des Ventils aus. Das TA-Smart-Ventil misst kontinuierlich die durch den Wärmeübertrager fließende Wärmeenergie und regelt den Durchfluss im Einspritzkreis. Die Durchfluss-, Temperatur-, Leistungs- und Energiedaten werden alle 15 Sekunden über ein 4G-Gateway an die IMI Hydronic Cloud gestreamt. Das Ventil macht die Anlagendaten transparent, indem es kontinuierlich umsetzbare Daten und Anpassungen bereitstellt und eine sehr gute Durchflussregelbarkeit gewährleistet. Das kompakte Ventil mit wenig Komponenten ermöglicht eine schnelle Installation mit geringen Umbaumaßnahmen und bietet eine laufende Systemanpassung. TA-Smart wird mit einer 24-V-Wechselstromversorgung betrieben und mit einem 10-V-Gleichstromsignal geregelt. Die Stromversorgung und das Reglersignal des 3-Wege-Ventilantriebs wurden wie ursprünglich installiert belassen.
Die zweite Systemaktualisierung erfolgte in Zusammenarbeit mit Enerbrain, indem in der Produktionshalle vier batteriebetriebene Sensoren an strategischen Stellen installiert wurden, die die relative Luftfeuchtigkeit, Temperatur und den CO2-Gehalt messen. Zudem wurde ebenfalls das Leitsystem um eine Cloud-Regelungs- und Visualisierungslösung erweitert. Dieses System passt die Sollwerte von Ventil, Ventilatoren und Klappen dynamisch gemäß den Mess- und historischen Daten des Sensors an und nutzt dafür moderne Analysealgorithmen. Dieses zweite System-Upgrade trägt dazu bei, die Systemtransparenz zu erhöhen, indem Daten auf konsolidierte Weise Verfügbar gemacht werden. Zudem passt das System auch dynamisch den Sollwert an, der das Problem der Schwankungen der Systemleistung adressiert.
Die komplette Installation dauerte einen Tag und wurde vom Wartungsteam des Werks durchgeführt. Zur Inbetriebnahme wurde das TA-Smart-Ventil ohne zusätzliche Geräte mit der HyTune App von IMI Hydronic Engineering parametriert. Der Regelmodus wurde auf Durchflussregelung eingestellt, um eine EQM-Charakteristik zu gewährleisten, die insbesondere auch im unteren Öffnungsbereich (bis 20 % der Durchflussmenge) eine sehr hohe Regelgenauigkeit sicherstellt. Der Auslegungsdurchfluss wurde auf 13.500 l/h angepasst. Da vor Ort keine Bus- oder internen Netzwerke verfügbar waren, wurde ein 4G-Gateway installiert, um Daten an die HyCloud zu streamen.
Ergebnis und Fazit
Zur Bewertung der Auswirkungen der Maßnahmen auf das Gesamtsystem, wurden zwei Phasen definiert. Phase 1: Simulation des Altsystems und Phase 2: Analyse des neuen Systems. Diese beiden Phasen wurden jeweils zwei Wochen lang durchgeführt. In der ersten Phase wurde nach der Installation der neuen Lösung TA-Smart auf Stellungsregelung eingestellt und das neue Regelungssystem ausgeschaltet. So konnte das Verhalten des alten 3-Wege-Ventils simuliert werden. In der zweiten Phase wurde TA-Smart in den Durchflussregelmodus versetzt und die Algorithmen wurden eingeschaltet. Der Vergleich zwischen den beiden Phasen zeigte während des einmonatigen Tests, dass mit dem neuen Regelungssystem beim thermischen Energieverbrauch etwa 45 % eingespart wurden und der Benutzerkomfort von 43 % auf 67 % verbessert wurde.