Mit neuen High-Tech-Anlagen will Sicherheitstechnik-Hersteller Telenot den Qualitätsstandard der eigenen Produktion weiter erhöhen.
Im Fokus stehen dabei 7-stellige Investitionen in neue Produktionsanlagen, wie beispielsweise eine Bolzenschweißmaschine, eine hochflexible THT-Linie zur Leiterplattenbestückung oder eine speziell konfigurierte Laserzelle. „Jede dieser High-Tech-Anlagen trägt zur Steigerung von Qualität und Produktivität bei und ist ein klares Bekenntnis für den Produktionsstandort Deutschland“, sagt Anja Wunderle von der Telenot-Geschäftsleitung.
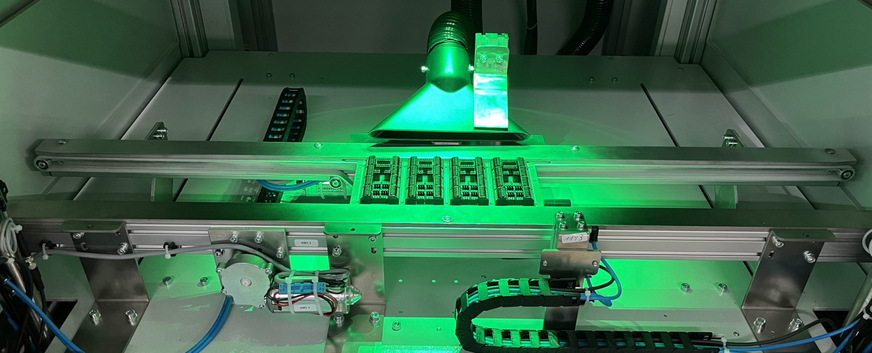
Telenot Electronic
Neue Bolzenschweißmaschine: Präzision in der Schweißtechnik
So sorgt seit wenigen Wochen im Telenot-Werk 2 in Essingen eine neue Bolzenschweißmaschine für eine höhere Effizienz und Präzision in der Produktion. Gewindebolzen mit Außengewinden, Gewindebuchsen mit Innengewinden, Flachstecker und Stifte werden hier auf verschiedene Metallteile wie Gehäusedeckel, Grundplatten, Frontplatten sowie Montageplatten geschweißt.
„Mit einer solchen modernen und flexiblen Anlage erhöhen wir nicht nur weiter unsere Fertigungstiefe, sondern werden bei steigender Präzision und Produktqualität auch noch schneller in der Fertigung“, erläutert Gesamtproduktionsleiter Jochen Hammel.
Hochflexible THT-Linie: Effizienz und Qualität in der Leiterplattenbestückung
In jedem Einbruch-, Brandmelde- oder Zutrittskontrollsystem von Telenot verbirgt sich ausgeklügelte Technologie. Dafür müssen unter anderem Leiterplatten mit Hunderten elektronischen Bauteilen bestückt werden. Der Prozess der Leiterplattenbestückung erfolgt bei Telenot schon seit Jahrzehnten nicht in Asien, sondern in Aalen-Hammerstadt. Im Anschluss an die SMD-Bestückung (Surface-Mounted Device) mit vier vollautomatischen Linien und zwei AOI-Systemen (Automatische Optische Inspektion), erfolgt die weitere Bestückung mit einer neuen THT-Linie (Through Hole Technology-Line). Ein modernes 3D-AOI-System zur Lötstellenkontrolle sowie eine innovative Wellenlötanlage mit Stickstoff-Volltunnel runden das Setup ab.
Die optische Bestückkontrolle an den Bestückarbeitsplätzen stellt sicher, dass die Leiterplatten fehlerfrei zur Wellenlötanlage weitergeleitet werden. Durch den Stickstoff-Volltunnel entsteht deutlich weniger Krätze im Tiegel, was wiederum den Wartungsaufwand um 90 % reduziert. Zusätzlich verringert sich durch die neue Anlage der Flussmittelverbrauch der Wellenlötanlage um etwa 75 %, und gleichzeitig verdoppelt sich die Durchlaufgeschwindigkeit der Lötrahmen. Dies ist ein enormer Nachhaltigkeitsaspekt, denn ein geringerer Flussmittelverbrauch und eine höhere Durchlaufgeschwindigkeit reduzieren den Materialverbrauch und vor allen Dingen den dafür notwendigen Energieeinsatz.

Telenot Electronic
Neue Laserzelle: Höhere Flexibilität und deutliche Variantenreduktion in der Beschaffung
Bevor Telenot seine eigens konfigurierte Laserzelle in Betrieb nahm, war die Klemmenbestückung von Leiterplatten mit erheblichen Herausforderungen verbunden. Bisher galt es, mehr als 44 unterschiedliche Varianten an Wago-Klemmen zu disponieren, was einen enormen Platzbedarf im Lager und eine latente Verwechslungsgefahr beim Lieferanten, im Wareneingang, im Lager sowie in der Produktion mit sich brachte und mit aufwendigen Kontrollschleifen überwacht werden musste. Mit der neuen Laserzelle sind nur noch sieben unbeschriftete Basisklemmen im Einsatz, die der Laser direkt auf den Leiterplatten individuell beschriftet – und das in Rekordzeit.
„In einem Vorgang können wir bis zu 60 Klemmen mit insgesamt 348 Zeichen oder Zahlen innerhalb von maximal fünf Sekunden markieren“, erklärt Jochen Hammel. Der eingebaute Hybridlaser der Firma Keyence kann zudem für die Beschriftung von Leiterplatten benutzt werden. Telenot ist im Moment die einzige Firma, die Klemmen in solch hoher Stückzahl auf Leiterplatten mithilfe eines Lasers individuell beschriftet.
Die höchste Investition tätigte Telenot für ein hochmodernes, neues Product Compliance Test-Center, das die Konformität aller Produkte mit den europäischen Normen prüft. Telenot ist einer der wenigen Hersteller, der ein solches Test-Center mit einer großen EMV-Messanlage (EMV = elektromagnetische Verträglichkeit) zur Produktprüfung betreibt.
➡️TÜV-Verband: Gut jeder zehnte Aufzug hat schwere Mängel
„Mit all unseren Investitionen stellen wir sicher, dass wir unseren Kunden immer die beste Qualität für unsere Sicherheitslösungen im Bereich der Einbruchmelde-, Brandmelde- und Zutrittskontrolltechnik für Privat und Gewerbe liefern. Durch die neuen Anlagen optimieren wir die Produktionsprozesse und stärken so unsere Wettbewerbsfähigkeit“, so Anja Wunderle. ■
Quelle: Telenot / ml