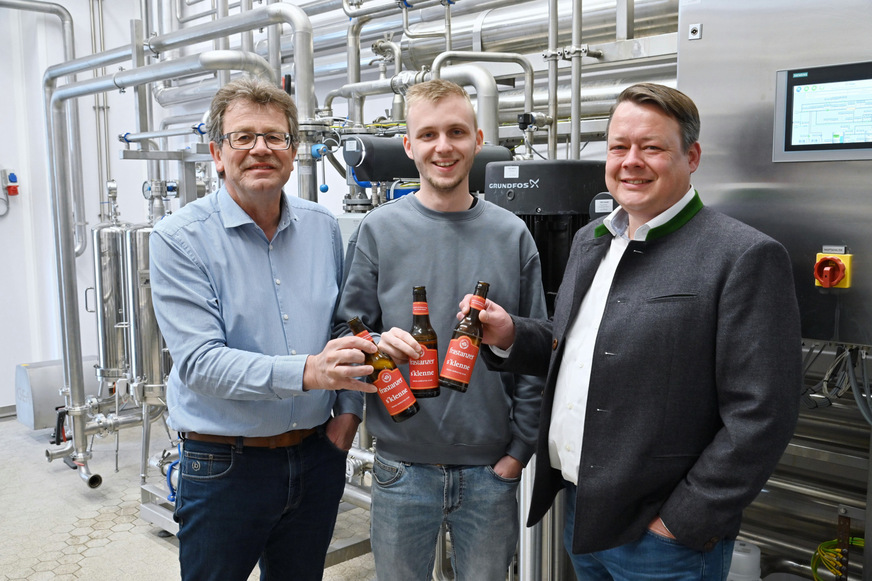
rünbeck
Die Traditionsbrauerei Frastanz hat seit einiger Zeit eine vollautomatische Wasseraufbereitungsanlage von Grünbeck in ihren Brauprozess integriert.
Die 1902 als Genossenschaft von 35 Wirten gegründete Brauerei Frastanz aus Vorarlberg setzt seit 2019 auf eine vollautomatische Wasseraufbereitungsanlage von Grünbeck. Die Anlage bereitet das harte Brunnenwasser auf, um die erforderliche, konstant hohe Wasserqualität für den Brauprozess zu erreichen. Dieser läuft seither effizienter und kostengünstiger als früher. Zudem schont das weichere Wasser die Anlagen, die dadurch deutlich weniger reinigungs- und wartungsintensiv sind.
Halbdurchlässige Membran trennt Härtebildner ab
Das System der Wasseraufbereitungsanlage basiert auf dem Prinzip der Umkehrosmose. Hierbei wird das Rohwasser mit einer Hochdruckpumpe durch eine halbdurchlässige Membran gepresst, welche fast ausschließlich Wassermoleküle passieren lässt. Nach dem Durchströmen der Membran wird das Wasser als Permeat (vollentsalztes Wasser) bezeichnet. Es ist nahezu frei von Kalk, Salzen, Schwermetallen, Partikeln sowie gelösten organischen Substanzen und sonstigen Verunreinigungen.
Das Konzentrat bleibt auf der anderen Seite der Membran mit den Härtebildnern, vor allem Calcium- und Magnesiumkationen, zurück. Um Härteausfällungen (Scaling), die die Poren der Membran zersetzen könnten, auf der Konzentrat-Seite zu verhindern, wird ein sogenanntes Antiscalant zugefügt. Das Konzentrat darf anschließend ohne neutralisiert zu werden direkt in das Entwässerungssystem fließen.
Das Permeat, von dem die Grünbeck-Anlage bis zu 12,5 m3 pro Stunde erzeugt, ist mit < 0,1 °dH deutlich weicher als für Brauwasser nötig. Daher verschneidet es die Brauerei automatisiert mit Brunnenwasser so, dass im Ergebnis die für den Brauprozess benötigte Härte von 3,5 bis 3,7 °dH erreicht wird. Zum Vergleich: Das Wasser hat vor der Aufbereitung eine Härte von 16 bis 17 °dH.
Um die Anforderungen an das Brauwasser zu erfüllen, musste die Brauerei früher einen hohen Aufwand betreiben. Lange setzte sie zur Enthärtung einen Kationenaustauscher ein. Diese Anlage mit einem Riesel-Entgaser benötigte viel Platz und war nicht automatisiert. Zudem benötigte sie zur Regenerierung viel Salzsäure – die beschafft, gelagert und gehandhabt werden musste.
Prozesse mit Wasseraufbereitungsanlage optimieren
Die Maischungs- und Gärungsprozesse haben sich laut Anton Schels, Technischer Leiter und 1. Braumeister, durch die Wasseraufbereitungsanlage verbessert. Das wirke sich auch auf die Kosten positiv aus. Aufgrund der neuen Brauwasserqualität war es möglich, das Dekoktions- auf ein Infusionsverfahren beim Maischen umzustellen. Im Sudhaus ist die enzymatische Wirkung dank der Wasseraufbereitung wesentlich besser, die Gärung verläuft merklich schneller. „Im Ergebnis wurde die Würze- respektive die Bierqualität und deren Geschmacksstabilität gesteigert“, so Schels.
Auch außerhalb des eigentlichen Brauprozesses profitiert Frastanz von der Anlage. Denn um Brauanlagen, Gär- und Lagertanks zu schonen, verwendet die Brauerei das aufbereitete Wasser nun auch als Prozesswasser in allen betrieblichen Teilbereichen. Das spart rund 30 % an Reinigungschemie ein. Zudem verkalken die Filtersysteme und Wärmetauscher weniger.
Mit Automatisierung betrieblichen Aufwand sparen
Der Aufwand für die jetzige Wasseraufbereitungsanlage ist minimal: „Wir schauen täglich einmal kurz auf die Anlage und die Daten, die uns die Steuerung anzeigt. Das dauert fünf Minuten. Ansonsten läuft die Anlage automatisch und völlig zuverlässig“, berichtet Schels.
Im Rahmen der Brauereimodernisierung stattete die Brauerei Frastanz die Anlage zudem mit einem neuen Sanitisierungs-Verfahren aus, welches eine Kontamination durch vereinzelte Keime in der Wasseraufbereitung verhindern soll. Denn mit dem Brunnenwasser können natürlich vereinzelte Keime in die Wasseraufbereitung gelangen und es gilt, diese zuverlässig zu eliminieren.
Mit der thermischen Sanitisierungs-Anlage wird einmal pro Monat ein auf etwa 80 °C erhitztes Permeat im Kreislauf durch die Anlage gepumpt. Zuvor wurde die Wasseraufbereitungsanlage aufwendig per Hand mit Reinigungs- und Desinfektionsmittel gesäubert. Das neue Vorgehen spart Zeit, Kosten für chemische Reinigungsstoffe und Personal. Für die thermische Sanitisierung mussten einige Anlagenteile durch hitzebeständige Ausführungen ersetzt werden. Um den Produktionsausfall möglichst gering zu halten, baute ein Team von Grünbeck die Anlage während der Verlagerung vor Ort um. Nach nur fünf Tagen konnte die Anlage wieder genutzt werden. ■
Quelle: Grünbeck / le / ml