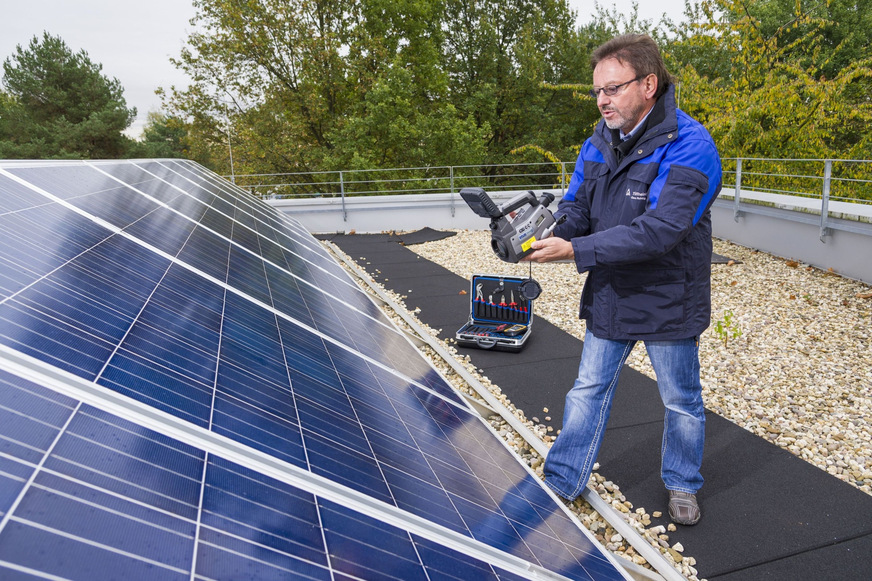
TÜV Rheinland
Montage-, Modul- oder Anschlussfehler können bei Photovoltaik-Anlagen Ertragseinbußen und sogar Brände auslösen. IR-Kameras spüren im laufenden Betrieb thermische Auffälligkeiten auf und helfen so, die Wirtschaftlichkeit und die Sicherheit von Photovoltaik-Anlagen zu erhöhen.
Der Artikel kompakt zusammengefasst
■ Gegenüber anderen Prüf- und Messverfahren hat die Thermografie von Photovoltaik-Anlagen den Vorteil, dass diese dafür nicht abgeschaltet werden müssen.
■ Mithilfe der Photovoltaik-Thermografie können durch Verschattungen, Verunreinigungen und andere Gründe verursachte Überhitzungen einzelner Zellen, fehlerhafte Module, Anschluss- oder Verschaltungsfehler unter Last detektiert und dokumentiert werden.
■ Auch geringe Teilausfälle, die die Rentabilität von Photovoltaik-Anlagen während ihrer Laufzeit durch Mindererträge verringern, werden erkannt.
■ Neben der Qualitäts- und Ertragssicherung dient die Photovoltaik-Thermografie auch dem vorbeugenden Brandschutz, denn Fehler an Modulen, Anschlüssen oder Elektrospeichern können im Extremfall Brände verursachen und Anlagen zerstören.
■ Neben einer guten IR-Kameratechnik setzt die PV-Thermografie allerdings Fachwissen und viel Erfahrung voraus.
Mit der aktuellen Boomphase in der zahlreiche kleine und große Photovoltaik-Anlagen errichtet werden, gewinnt auch deren Wartung und Instandhaltung an Bedeutung. Neben anderen Messverfahren kommt dabei schon seit vielen Jahren die Infrarot-Thermografie zum Einsatz. Sie zeigt im laufenden Betrieb unter Last thermische Auffälligkeiten und Fehler visuell an und kann damit die Qualität, Produktivität und Sicherheit von Photovoltaik-Anlagen überwachen.
Vieles, was dem Auge verborgen bleibt, kann per Infrarottechnik lokalisiert und dokumentiert werden: Fehlerhafte Module oder Anschluss- und Verschaltungsfehler direkt nach der Montage, durch Verschattungen, Verschmutzungen und andere Gründe verursachte Überhitzungen einzelner Zellen oder schadhafte Kontakte, Kabel, Sicherungen, Schalter, Wechselrichter und Stromspeicher.
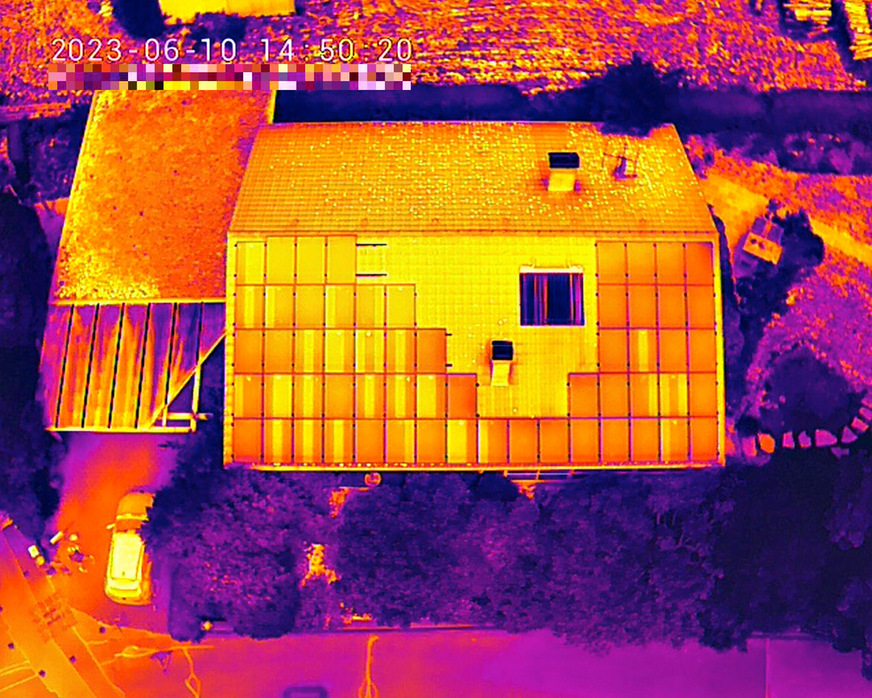
Drohnenbilder-Weiden
Stimmt die Leistung noch?
Defekte und Funktionseinschränkungen von Photovoltaik-Anlagen lassen sich als thermische Auffälligkeiten auf dem IR-Kameradisplay als Hotspots (heiße Stellen) lokalisieren. Sie entstehen beispielsweise dadurch, dass verschattete oder defekte Modulzellen einen internen elektrischen Widerstand bilden. So wird aus einer Modulzelle, die im Normalfall Strom erzeugt, ein Stromverbraucher, der sich lokal erwärmt und so thermische Auffälligkeiten verursacht. Die Zelle kann sich dabei so stark erhitzen, dass sie und umgebende Bereiche beschädigt werden.
Bypassdioden schützen zwar Solarzellen vor einer Überhitzung. Versagt allerdings eine defekte oder bei geringer Verschattung nicht ansprechende Bypassdiode ihren Dienst, kommt es zu unkontrollierten Hotspots. Defekte an Bypassdioden entstehen beispielsweise, wenn in der Planungsphase durch bauliche Anlagen oder die Vegetation bedingte Verschattungen nicht berücksichtigt werden. Dann stehen Modulzellen und Bypassdioden unter Dauerbelastung und versagen über kurz oder lang.
Auch der Wirkungsgrad einer Solaranlage hängt von der Modultemperatur ab. Erwärmen sich PV-Module aufgrund von Verschattungen oder defekten Zellen, fällt der Wirkungsgrad um etwa 0,5 %/K. Eine Erwärmung um nur 10 K gegenüber der mittleren Normaltemperatur hat somit eine um 5 % geringere Stromausbeute zur Folge. Schon diese geringen Teilausfälle können zu Mindererträgen führen, die eine Anlage während einer 20-jährigen Laufzeit unrentabel machen.
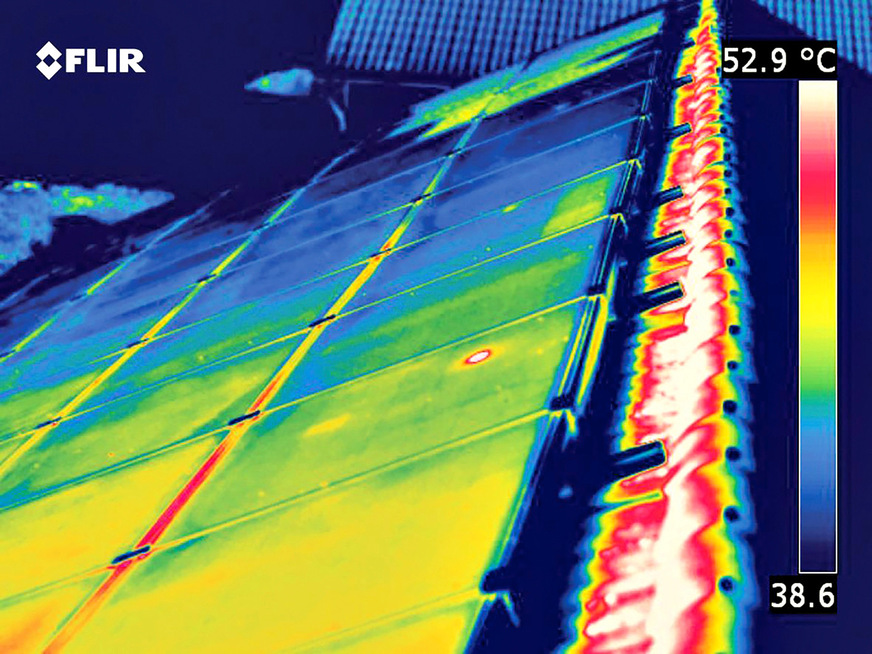
Teledyne Flir
Was leisten IR-Kameras bei der Thermografie von Photovoltaik-Anlagen?
Zwar sind einige herstellungs- oder installationsbedingte Fehler wie Zelleinschlüsse, Zellrisse, Schichtablösungen oder fehlerhafte Kabelanschlüsse auch optisch erkennbar. Vieles bleibt dem Auge aber verborgen und wird erst messtechnisch nachweisbar: So kann man etwa mit einer Kennlinienmessung einzelne Module oder Modulstränge genauer untersuchen. Dabei muss jedoch in den Stromkreis eingegriffen werden, was aufwendig ist und den Anlagenbetrieb stört. Auch Anlagenüberwachungssysteme und Datenlogger zur kontinuierlichen Aufzeichnung von Anlagendaten ermöglichen Qualitätskontrollen. Damit lassen sich jedoch nur Verluste ab einem 1 kW erkennen.
Die berührungslose und zerstörungsfreie Thermografie-Messtechnik deckt auch kleinere Fehler bis auf die Modulzellen-Ebene auf. Sowohl kleine, private Dachanlagen als auch sehr große gewerbliche Solarparks mit mehreren MW Leistung lassen sich mit einem Kameraschwenk, gegebenenfalls auch per Drohne, großflächig scannen, um thermische Auffälligkeiten schnell zu erfassen. Auch alle anderen Anlagenkomponenten wie elektrische Verbindungen, Wechselrichter oder Stromspeicher können thermografisch überprüft werden. Sinnvoll sind Überprüfungen sowohl unmittelbar nach der Anlagen-Inbetriebnahme (und vor Ablauf der Gewährleistung) als auch im Rahmen regelmäßiger Inspektionen.
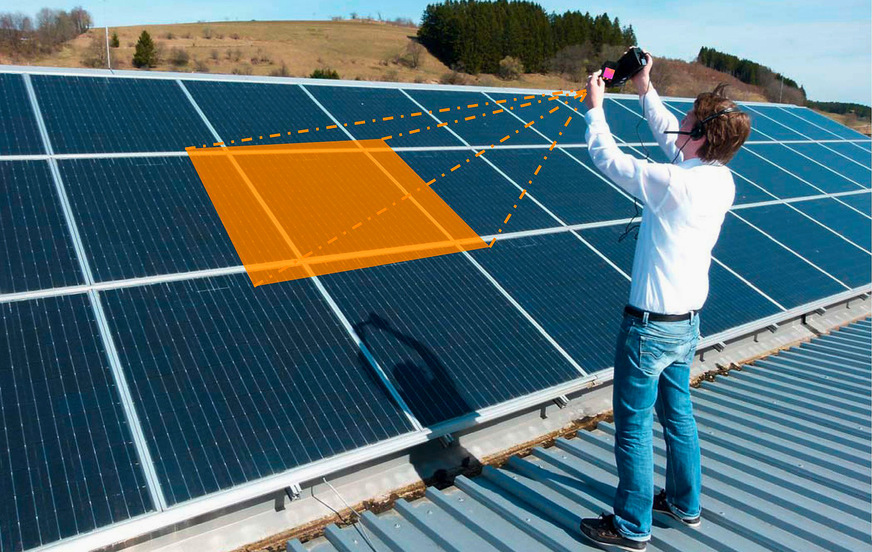
Testo
Die Rahmenbedingungen während der Messung müssen stimmen
Die wichtigste Voraussetzung für eine thermografische Untersuchung von PV-Modulen ist eine ausreichende Sonneneinstrahlung. Das ist die momentane flächenspezifische Energieeinwirkung auf eine Fläche. Sie lässt sich beispielsweise mit einem einfachen Photodetektor oder einem präziseren Pyranometer (Sonneneinstrahlungs-Messgerät), möglichst unmittelbar am Solarmodul messen. Die Einstrahlungsleistung sollte notiert werden, damit man die Messwerte zum Beispiel auf die Nennlast hochrechnen kann. Einen ausreichenden thermischen Kontrast für die Inspektion von Solarzellen vor Ort erhält man bei einer Sonneneinstrahlung von mindestens 600 W/m2.
Bestimmte Messaufgaben, etwa die Überprüfung von Dünnschichtmodulen mit geringem Wirkungsgrad, können höhere Strahlungsintensitäten ab 800 W/m2 erfordern. Da Wolken die Sonneneinstrahlung verringern und zusätzlich störende Reflexionen verursachen, sollte der Himmel möglichst wolkenlos sein (maximal 2/8 Cumulus). Nach schnellen Einstrahlungs-, respektive Lastwechseln sollten Einschwingzeiten von mindestens 10 min abgewartet werden.
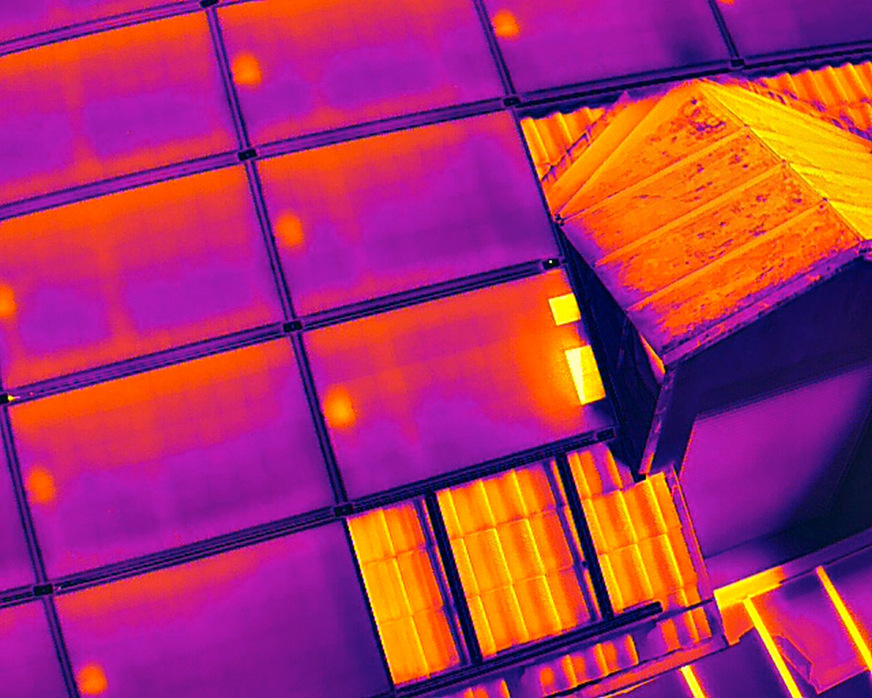
Drohnenbilder-Weiden
Werden Solarmodule zusätzlich auch von der Rückseite aufgenommen, lassen sie sich sicherer analysieren und interpretieren. Störende Effekte wechselnder Sonneneinstrahlung lassen sich durch die sogenannte Rückstromthermografie beseitigen. Dabei wird nachts die Photovoltaikanlage an ein externes Netzteil angeschlossen, das einen Strom in Gegenrichtung zur normalen Fließrichtung erzeugt. Fehler in den Solarmodulen können auf diese Weise aufgespürt werden, allerdings keine punktuellen Verschmutzungen oder Beschädigungen.
Auch Wind und Luftströme auf der Solarmodul-Oberfläche können zu falschen Messungen führen – in diesem Fall durch eine konvektionsbedingte Abkühlung. Deshalb sollte die Windstärke einen Beaufortgrad von höchstens 4 (mäßige Brise, 20 bis 28 km/h; Wind bewegt Zweige und dünnere Äste, hebt Staub und loses Papier) betragen. Je niedriger die Lufttemperatur ist, desto höher ist der erzielbare thermische Kontrast. Eine optimale Tageszeit für thermografische Untersuchungen sind im Sommer deshalb frühe Morgenstunden, sofern die Sonneneinstrahlung ausreicht.
Bei kleinen Dachanlagen sind manchmal eine Leiter oder das gegenüberliegende (Dach-)Fenster des Nachbarhauses nützlich, um eine geeignete Aufnahmeposition zu erhalten. Drohnen ermöglichen beliebige Aufnahmeperspektiven und auch sehr große Anlagen können schnell erfasst werden (siehe auch Info-Kasten). Im Vorfeld solle man sich Informationen über die Zugänglichkeit der Anlage sowie Wetterprognosen, ergänzt durch Echtzeit-Wolken-/Regenradarbilder einholen (z. B. über Google Maps, Wetteronline etc.).
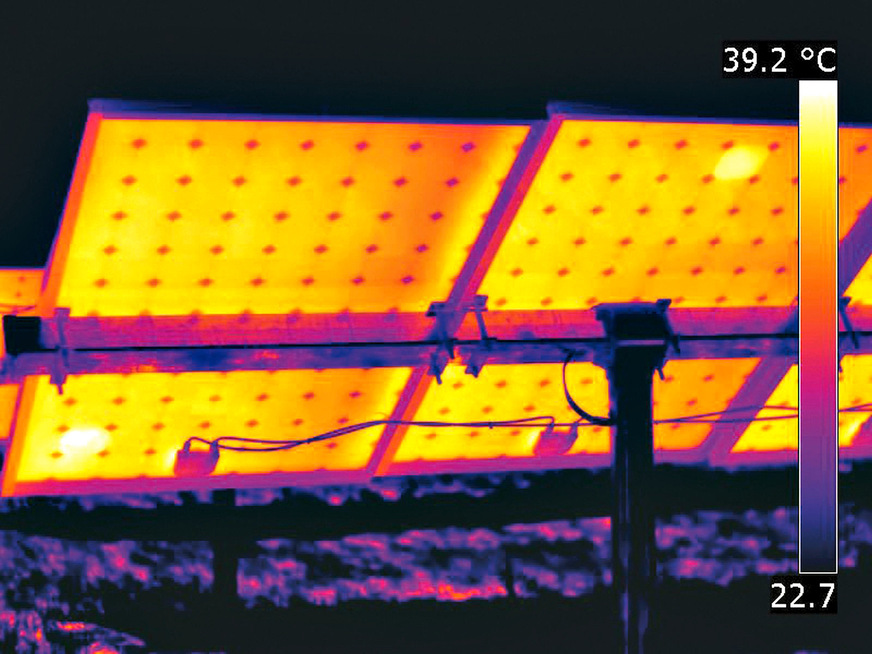
Teledyne Flir
Potenzielle Fehlerquellen
In der Regel werden Photovoltaik-Anlagen im Lastbetrieb untersucht. Je nach Solarzellentyp und Art des Defekts können aber auch Messungen im Leerlauf oder Kurzschluss zusätzliche Informationen liefern. In jedem Fall sollte man vor einer thermografischen Untersuchung den Betriebszustand der Anlage erfassen – entweder am Wechselrichter-Display, mit einer Stromzange oder durch Abschattung einer Modulzelle. Wird diese nach etwa einer halben Minute warm, ist die Anlage in Betrieb.
Bei der Temperaturmessung müssen mehrere Parameter eingestellt, respektive bei der Interpretation berücksichtigt werden: Dazu gehören unter anderem der materialspezifische Wärmeabstrahl-Kennwert (Emissionsgrad) des jeweiligen Moduls und die reflektierte Temperatur. Weitere, für die Messung und Interpretation relevante Parameter können der Objektabstand, die Windgeschwindigkeit, die Luftfeuchtigkeit, die Sonneneinstrahlung auf Generatorebene, der Modul-Wirkungsgrad und andere Faktoren sein.
Da es bei der Untersuchung von Photovoltaik-Anlagen vor allem auf ein qualitatives Abbild der Wärmeverteilung der Module ankommt, um so eventuelle Defekte und Fehlfunktionen zu lokalisieren, ist die Messung absoluter Temperaturen eher von sekundärer Bedeutung.
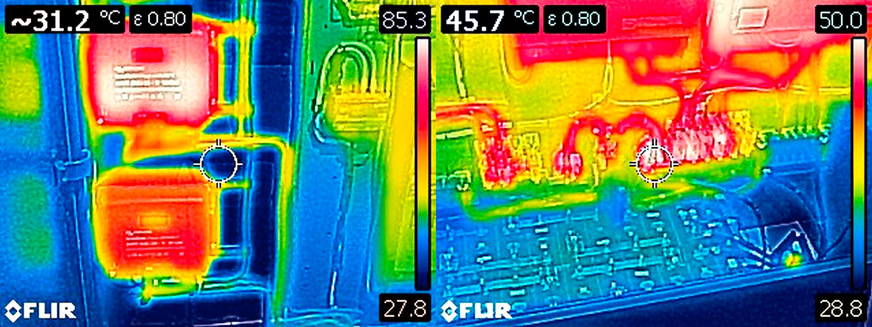
Markus Steiner
Bei der Aufnahme sollten Modulbereiche möglichst nicht von Objekten verschattet werden oder diese sich im Modul spiegeln. Schatten auf PV-Modulen führen nicht zu einer Abkühlung an dieser Stelle, sondern zu einer Erwärmung. So können Schattenwürfe fälschlicherweise als Modulfehler gewertet werden. Auch ein zu kurzes Abwarten nach einer Wolkenverschattung kann zu einer Fehlinterpretation bei vorhandenen Fehlern führen. So fallen einige Module oder Modulstränge erst aus, nachdem eine bestimmte Betriebstemperatur erreicht wurde. Ferner sollten Sonnenstrahlen nicht in Kamerarichtung reflektiert werden, da Sonnenreflektionen ebenfalls als vermeintliche Hotspots interpretiert werden können.
Da sich manche Fehlerbilder bei der PV-Thermografie ähneln, sollte man diese, zum Beispiel anhand einer Fehlerbild-Tabelle, näher untersuchen. Beispielsweise können eine Verschmutzung und ein Diodenausfall ein ähnliches Fehlerbild zeigen. Bei der Aufnahme sollte man beachten, dass der Aufnahmewinkel zum PV-Modul nicht zu flach ist, sonst besteht die Gefahr, dass nach dem Prinzip „Einfallswinkel gleich Ausfallswinkel“ der umgebende Himmel thermografiert wird, weil die Moduloberfläche wie ein Spiegel wirkt. Optimal ist ein nahezu rechter Winkel mit einer Abweichung von 5 bis 10° zur Kollektorebene.
Da IR-Kameradetektoren empfindlich gegenüber direkter Sonneneinstrahlung sind, ist Vorsicht bei der Ausrichtung des Kameraobjektivs geboten. Alle IR-Aufnahmen sollten zusätzlich durch Digitalkamera-Fotos dokumentiert werden, um die spätere Auswertung und Interpretation zu vereinfachen. Bei größeren Anlagen solle man einen Anlagen- und Stringplan mitführen. Er hilft, die besten Kamerastandpunkte auszuwählen und die Übersicht zu behalten über bereits erfasste Bereiche und alle lokalisierten Fehler.
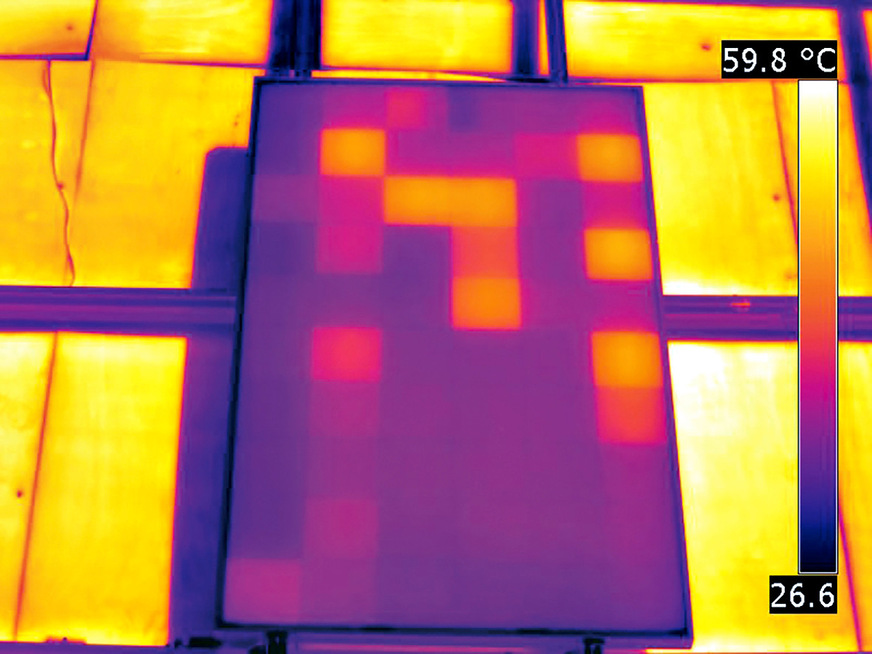
Teledyne Flir
Auswertung und Berichterstellung
Für die Auswertung, Optimierung und Nachjustierung der Thermogramme und deren Zusammenstellung zu aussagekräftigen und nachvollziehbaren Berichten offerieren die Anbieter von IR-Kameras spezielle Auswertungsprogramme. Diese unterstützen Thermografen beim anspruchsvollsten Teil der PV-Thermografie. Es können zum einen Messfehler (zu flacher Aufnahmewinkel, Änderung der Sonneneinstrahlung, Reflexionen etc.) zu Fehlinterpretationen führen. Zum anderen ist Photovoltaik-Fachwissen nötig (Modul-Art und -Herstellung, Solarzellen- und Modulaufbau, Anlagenbau, Verschaltung etc.). Nicht zuletzt ist Erfahrung erforderlich, um echte Schäden von durch Reflexionen oder temporäre Einflüsse bedingten Effekten unterscheiden und richtig einschätzen zu können.
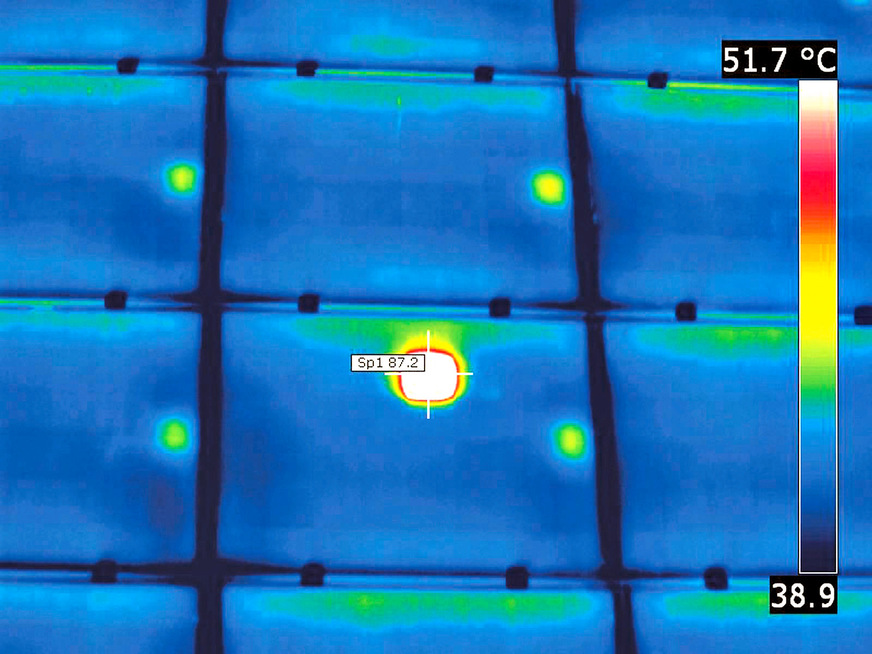
Teledyne Flir
Viele Anomalien lassen per se nicht auf eine eindeutige Fehlerursache schließen. Während die Erwärmung mehrerer einzelner Zellen in einem Modul („Patchwork-Muster“) meist durch Defekte, interne Kurzschlüsse etc. verursacht wird, kann ein einzelner Hotspot im PV-Modul sowohl auf eine, etwa durch eine Verschmutzung bedingte, partielle Abschattung als auch auf einen Zellriss hinweisen. Lässt die IR-Aufnahme keine eindeutige Interpretation zu, muss mit anderen Methoden (Sichtprüfung, elektrische Kennlinienmessung etc.) nach der Fehlerursache gesucht werden.
Zu den weiteren typischen Fehlerbildern gehören einzelne oder zufällig verteilte Zellen mit Übertemperatur, erwärmte Zellenstränge, falsch angeschlossene Module oder Module im Leerlauf, erwärmte Anschlussdosen und so weiter (siehe auch [4]). Diese müssen korrekt interpretiert und gemäß DIN 54191 [1] im Thermografiebericht in Fehlergruppen eingeteilt und konkrete Handlungsempfehlungen ausgesprochen werden, z. B.: „keine akuten Maßnahmen“ oder „Ursachenprüfung, einschließlich Beseitigung innerhalb von zwei Monaten“.
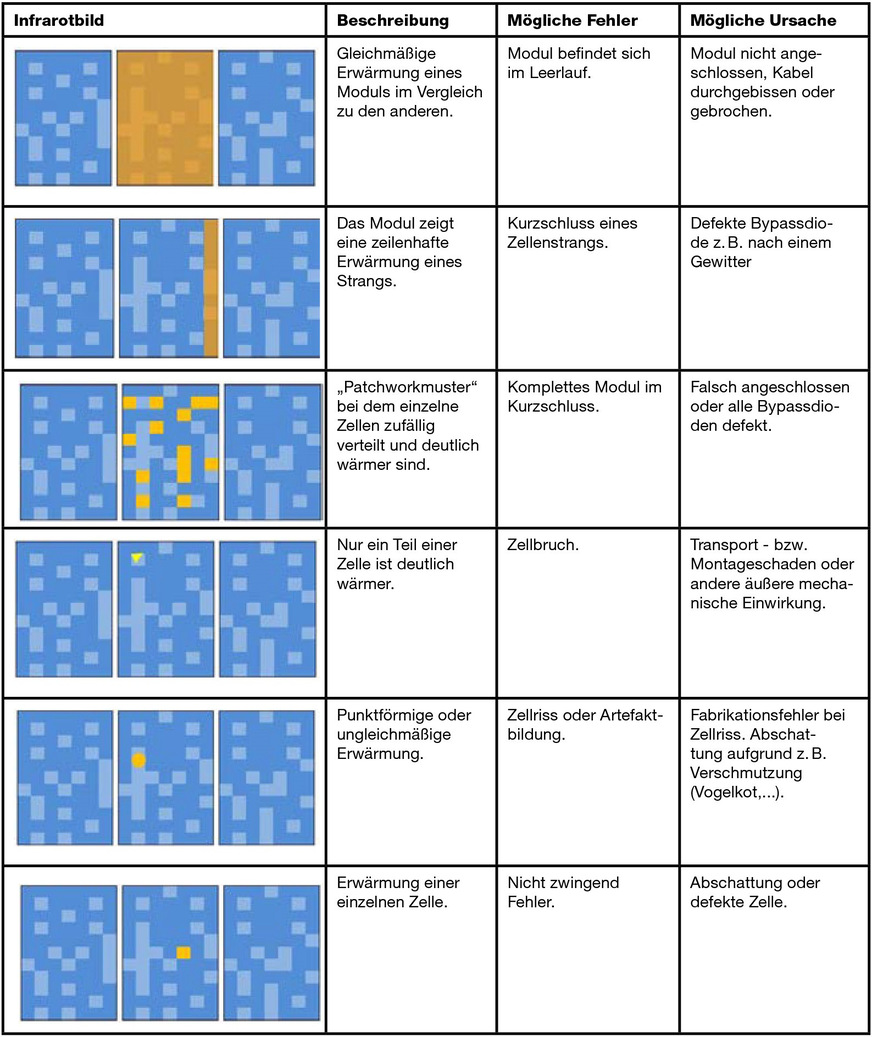
Testo
PV-Thermografie und Brandschutz
Die PV-Thermografie dient nicht nur der Qualitätssicherung und Produktivitätskontrolle. Sie ermöglicht auch einen vorbeugenden Brandschutz, denn Modul- oder Anschlussfehler können im Extremfall Brände auslösen. Solange Licht auf die Module fällt, produzieren PV-Anlagen Strom. Löst sich zum Beispiel eine Steckverbindung, kann aufgrund der hohen Spannungen ein Lichtbogen entstehen, der einen Brand auslösen kann.
Bei Dach-Anlagen entsteht zwischen der Dachhaut und den PV-Modulen ein Kamineffekt, der den Brand verstärken kann. Bei der Verbrennung entstehen außerdem aufgrund der verbauten Werkstoffe giftige Gase. Im Brandfall entstehende Splitter und die hohen Gleichspannungen bilden mit dem Löschwasser eine weitere Gefahrenquelle. Auch bei Wechselrichtern und anderen elektrischen Komponenten können Materialdefekte oder eine unsachgemäße Montage und Verschaltung zu einer Brandgefahr werden. Auch bei der Photovoltaik gilt deshalb: Vorbeugen ist besser als Löschen. Weitere Infos: www.pv-brandsicherheit.de
Anforderungen an die Kameratechnik
Neben Fachwissen und Erfahrung setzt die PV-Thermografie auch eine gute IR-Kameratechnik voraus. So sollte die Kamera über eine thermische Empfindlichkeit (NETD-Wert) von mindestens 0,08 K verfügen, damit auch kleine Temperaturunterschiede aufgedeckt werden können. Die Detektorauflösung sollte mindestens 320 × 240 IR-Messpunkte erfassen. Besser geeignet sind Modelle mit höherer thermischer Empfindlichkeit (ab 0,06 K) und Detektorauflösung, beispielsweise 640 × 480 IR-Pixel und mehr.
Sinnvoll ist eine Wechseloptik, damit man sowohl Detail- als auch Übersichtsaufnahmen machen kann. Ein dreh- und schwenkbares LC-Display ermöglicht Über-Kopf-Aufnahmen. Außerdem sollte die Kamera über einen optischen Sucher verfügen, denn bei starker Sonneneinstrahlung ist auf den LC-Displays kaum etwas erkennbar. Eine eingebaute oder separate, möglichst hoch auflösende optische Digitalkamera erleichtert die Zuordnung und Auswertung der Thermogramme. Parameter wie Level und Span sollten manuell regelbar sein, um den thermischen Kontrast optimal einstellen zu können.
Weitere nützliche Kamerafunktionen können die Aufzeichnung von Sprachnotizen oder die GPS-Verortung von Wärmebildern sein. Damit lassen sich fehlerhafte Module in großen Freiflächenanlagen einfacher lokalisieren und Infrarotaufnahmen einfacher den Modulen zuordnen. Die Bedienperson sollte Kenntnisse aus der Bau-, PV- und Elektro-Thermografie mitbringen; über die Kamerabedienung hinaus mögliche Fehlerquellen und Grenzen der Thermografie kennen und Messergebnisse korrekt interpretieren können. Messpersonal, das nach DIN EN ISO 9712 [3] oder VdS 2859 [6] zertifiziert ist, verfügt über entsprechendes Know-how.
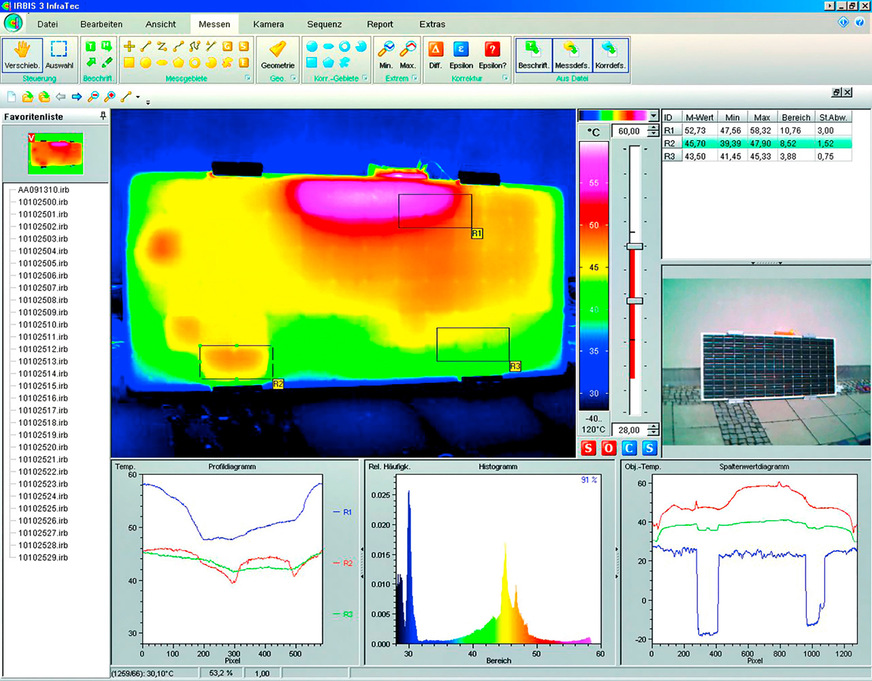
InfraTec
Selber machen oder beauftragen?
Die Thermografie hat sich in der Photovoltaik als zeitsparende und wirtschaftliche Messmethode etabliert und bewährt. Allerdings sollte man berücksichtigen, dass sicherheitsrelevante Probleme womöglich erst bei hohen Belastungen auftreten. Läuft eine Anlage deutlich unter Volllast, werden Gefahren unter Umständen nicht erkannt. Thermografie-Untersuchungen sind deshalb kein Ersatz für wiederkehrende Sichtkontrollen, Funktionsprüfungen oder Strommessungen, sondern lediglich eine Ergänzung.
Wärmebilder sind außerdem immer nur eine Momentaufnahme – deshalb sind insbesondere bei Großanlagen wiederholte thermografische Überprüfungen (z. B. jährlich oder zweijährlich) sinnvoll. PV-Thermografie-taugliche IR-Kameras kosten um die 5000 Euro – und mehr. Die Gerätemiete beträgt, je nach Modell und Mietdauer, zwischen 40 und 200 Euro/d zuzüglich Versand, Versicherung und ggf. Kaution. Eine in der Regel zweitägige PV-Thermografie-Schulung kostet ca. 600 Euro, zuzüglich einer Zertifizierungsgebühr (ca. 100 Euro).
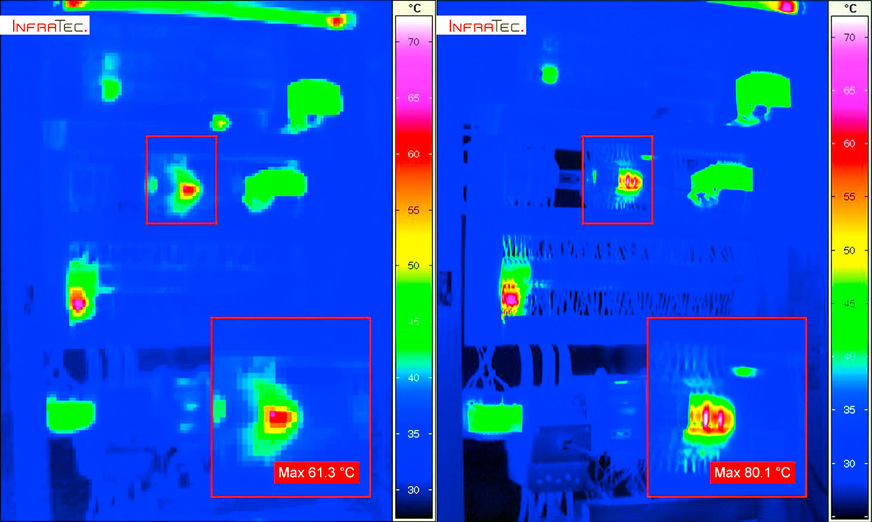
InfraTec
Die Kosten für eine PV-Thermografie-Dienstleistung hängen vom Leistungsumfang, vom Messobjekt, der Aufgabenstellung, der Zugänglichkeit und Anreisedauer zur Anlage sowie weiteren Faktoren ab. Für eine durchschnittliche Dachanlage eines Einfamilienhauses fallen in der Regel Kosten von 400 bis 500 Euro an. Für größere Anlagen sollte man ein Angebot von einem zertifizierten, auf die PV-Thermografie spezialisierten Dienstleister einholen. Kompetente Thermografen sind beispielsweise auf www.vath.de und www.vds.de/zertifikate/verzeichnis/V2861 gelistet. Marian Behaneck
PV-Thermografie in der Praxis
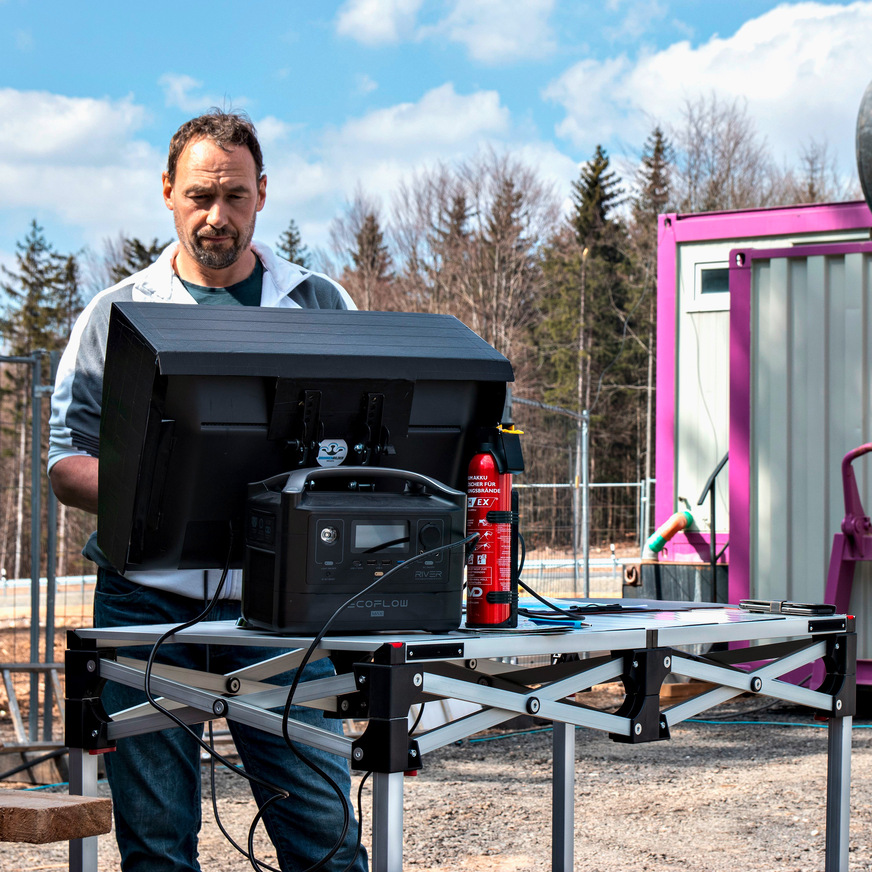
Drohnenbilder-Weiden
Peter Wurm, zertifizierter UAV-Fernpilot und Inhaber von Drohnenbilder-Weiden aus Püchersreuth, sieht in der PV-Thermografie noch viel Potenzial: „Unserer Erfahrung nach könnten mindestens 80 % aller privaten oder gewerblichen PV-Anlagen mehr Leistung bringen, wenn man defekte Module erkennen und austauschen würde. Auch unmittelbar nach der Installation weisen viele Anlagen Mängel auf, etwa falsch oder gar nicht angeschlossene Module. Zudem kann es bei unsachgemäßer Montage zu Spannungen und Folgeschäden im Modul kommen.“
Als Anbieter für Drohneninspektionen kennt Wurm die Vorteile der Drohnen-Thermografie gegenüber Handkameras: „Ein idealer, nahezu senkrechter Kamerawinkel zur Kollektorebene kann im Gegensatz zu Handkameras problemlos eingehalten werden. Die Anlage muss nicht betreten werden und kann entsprechend vorgegebener Wegpunkte, welche die Drohne selbständig überfliegt, sehr schnell erfasst werden. So können beispielsweise 18 ha in etwa 2,5 h beflogen werden, inklusive eventuellem Akku- und Speicherkartenwechsel etc.“
Beim Überflug muss darauf geachtet werden, dass die Drohne keinen Schatten auf noch zu messende Bereiche wirft, da dies sonst zu einer Erwärmung an diesen Stellen führt. Zum Equipment von Peter Wurm gehört eine Wärmebildkamera mit hoher Auflösung von 640 × 512 IR-Pixel (DJI Zenmuse H20N, ca. 12 000 Euro), die an einer Multicopter-Drohne (DJI Matrice M300, ca. 10 000 Euro) befestigt ist. Wenn den ganzen Tag geflogen wird, gehören zu einem kompletten, einsatzfähigen System 10 Akkus, die wechselweise eingesetzt und geladen werden. Geladen werden diese über eine mobile, vom Stromnetz autarke PV-Anlage.
Ein zusätzliches RTK-Modul ermöglicht eine zentimetergenaue Drohnen-Positionierung. Dies ist wichtig bei PV-Anlagen in der Nähe einer Autobahn, um den gesetzlich vorgeschriebenen Abstand zur Autobahn einhalten zu können. Das komplette System kostet ca. 25 000 Euro. Eine PV-Thermografie per Drohnenflug für ein Einfamilienhaus mit einer 10 kWp Anlage in Stadtrandlage, inklusive Protokoll und Anmeldung bei Ordnungsamt, Polizei, Absicherung und Fallschirm kostet rund 380 Euro brutto. Bei Freiflächenanlagen wird nach Stundensatz abgerechnet. Dieser Stundensatz beinhaltet den Piloten inklusive Fluggerät, Akkuladung, Ausrüstung und liegt bei 70 Euro. Hinzu kommen Kosten für die Auswertung und das Protokoll. www.drohnenbilder-weiden.de
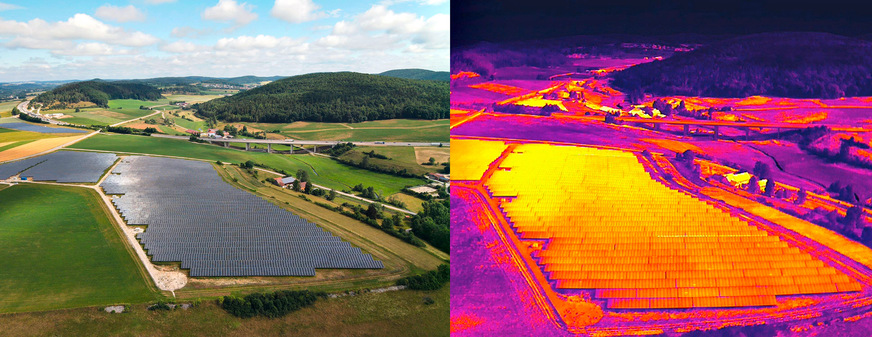
Drohnenbilder-Weiden
Fachberichte mit ähnlichen Themen bündelt das TGA+E-Dossier Thermografie
Literatur
[1] DIN 54191 Zerstörungsfreie Prüfung – Thermografische Prüfung von elektrischen Anlagen. Berlin: Beuth Verlag, Oktober 2017
[2] DIN IEC/TS 62446-3 Photovoltaik(PV)-Systeme – Anforderungen an Prüfung, Dokumentation und Instandhaltung – Teil 3: Photovoltaische Module und Betriebsanlagen – Infrarot-Thermografie im Freien. Berlin: Beuth Verlag, April 2018
[3] DIN EN ISO 9712 Zerstörungsfreie Prüfung – Qualifizierung und Zertifizierung von Personal der zerstörungsfreien Prüfung. Berlin: Beuth Verlag, September 2022
[4] VATh-Richtlinie Elektrothermografie: Niederspannung. Elektrothermografie zur Planung, Durchführung und Dokumentation infrarot-thermografischer Messungen an elektrischen Anlagen und Bauteilen ≤ 1 kV AV bzw. 1,5 kV AV. Nürnberg: Bundesverband für Angewandte Thermografie, 2018
[5] VdS 2858 Thermografie in elektrischen Anlagen – Ein Beitrag zur Schadenverhütung und Betriebssicherheit. Berlin: Beuth Verlag, November 2017
[6] VdS 2859 VdS-Richtlinien für die Anerkennung von Sachverständigen für Elektrothermografie (Elektrothermografen). Berlin: Beuth Verlag, Mai 2019
[7] Abschlussbericht der Machbarkeitsstudie zur Überprüfung der Qualität von Photovoltaik-Modulen mittels Infrarot-Aufnahmen. Erlangen, ZAE Bayern 2007
[8] Weinreich B., Schauer B., Gürzing, S., Haas R.: Fallstudie 2.0 zur Modul- und Anlagenqualität auf Basis thermografischer Messungen von 1 GW. Gauring-Hausen: 2019
[9] Schulungsunterlagen zum Seminar PV-Thermografie. Dresden: InfraTec (Hrsg.), 2014
[10] Praxisratgeber Thermografie für Photovoltaik-Anlagen. Titisee-Neustadt: Testo (Hrsg.), 2018, Download: www.testo.com/de-ch/anwendungen/solar-energy-guide
[11] IR-Kamera-Anbieter (Auswahl):
www.bosch-professional.com
www.dias-infrared.de
www.dji.com
www.flir.de
www.fluke.de
www.hikmicrotech.com
www.infratec.de
www.irpod.net
www.pce-instruments.com
www.testboy.de
www.testo.de
www.thermal.com
www.trotec.de
[12] PV-Thermografie-Dienstleister (Auswahl):
www.dronebrothers.de
www.drohneninspektionen-brandes.de
www.drohnenbilder-weiden.de
www.flying-detection.com
www.kitawa.de
www.pv-reinigung.eu
www.sauer-engineering.de
www.tuv.com/germany/de
www.vizaar.de